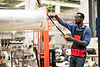
INDUSTRIAL ACCIDENTS
Although a wide range of industrial jobs are necessary to complete a variety of tasks, workers who fill roles – such as manning chemical plants and warehouses – face an increased risk of injuries on the job. Heavy machinery, toxic chemicals, and rigorous tasks combine to create a workplace environment that can quickly become dangerous if due diligence is not observed. Employers who cut corners when it comes to safety equipment put their workers at risk and it’s almost always the workers who pay the price.
Reliance on heavy machinery, while helpful, contributes to an alarming number of injuries in various fields. Workers can be caught in between moving parts, burned, or electrocuted, and the force behind a machine’s movements can make even a small error result in a serious injury. Industrial machinery accounts for the majority of injuries to workers’ hands and fingers, contributing a large percentage of amputations each year.
-
Lack of proper worker training to know when to use the equipment and how to use it safely. Workers have to know under which circumstances safety equipment is necessary, the type of equipment they should be using, the limitations of the equipment, and the proper care, maintenance, and disposal of all safety equipment on the premises.
-
Fumes and other toxic materials can cause harm ranging from single disastrous incidents to severe diseases developed through long-term exposure. The lungs, eyes, and skin are susceptible to chemical exposure. As such, equipment must be used regularly to minimize contamination. The Occupational Safety & Health Administration (OSHA) has determined the maximum amount of safe exposure to known dangerous toxins a worker may face over a length of time, and these permissible exposure limits (PELs) vary for each chemical.
-
With the prevalence of refineries here, Texas has a history of chemical accidents, perhaps the most notorious in recent years being the fertilizer plant explosion in West, Texas. While the Clean Air Act requires the Chemical Safety Board to investigate fires, explosions, or leaks, there is no regulation in place that requires the disclosure of these accidents, making it that much more difficult to learn from and prevent similar incidents in the future.
-
Training is vital and should be conducted for everything from safe ergonomic and lifting practices to how to correctly respond to fires and explosions.
The damages inflicted on workers in an industrial capacity can vary widely, ranging from minor lacerations to permanent paralysis. To minimize the risks posed by machinery, fumes, and other occupational hazards, equipment such as hard hats, goggles, glasses, faceplates that are appropriately shielded, masks, respirators, coveralls, gloves, and boots with adequate toe protection should be worn. It’s important that all gear fits correctly and is not too loose.
ACCORDING TO OSHA, ALL SAFETY EQUIPMENT NECESSARY TO PREVENT INJURY MUST FOLLOW SEVERAL REGULATIONS:
-
Safety equipment should be of a safe design and construction
-
Equipment must be maintained properly according to manufacturer’s specifications
-
Equipment should always be clean and reliable, meaning the equipment is in proper working order at all times and is readily accessible by every worker who may need it
-
Employers are not allowed to alter or modify safety equipment in any way, even if the employer believes such alterations may increase productivity
Besides safety equipment, certain processes should be put in place to help promote a safe work environment. There should be daily team updates on pertinent news or challenges. Any evacuation plans need to be taught to all personnel. Managers should constantly be evaluating the safety of the worksite and making changes as necessary. Safety signs should be posted to warn employees of dangers that might not be obvious, like toxic or hazardous materials, live wires, or falling objects. In the event of an emergency or accident, employees need to know what to do. Having written fire safety plans, accident reporting plans, and other types of workplace procedures can greatly help in the event of an accident.
Unfortunately for workers, some companies decide to put profits before safety. When companies ignore safety regulations, workers are the ones that suffer. While workplace industrial accidents happen every day, they are the result of the negligence of an employer or other responsible party. These companies should be held accountable for the pain and suffering they have caused and prevented from hurting more American workers.
COMMON ITEMS AND CONDITIONS THAT CONTRIBUTE TO INDUSTRIAL ACCIDENTS INCLUDE:
SERVING HOUSTON'S INJURED
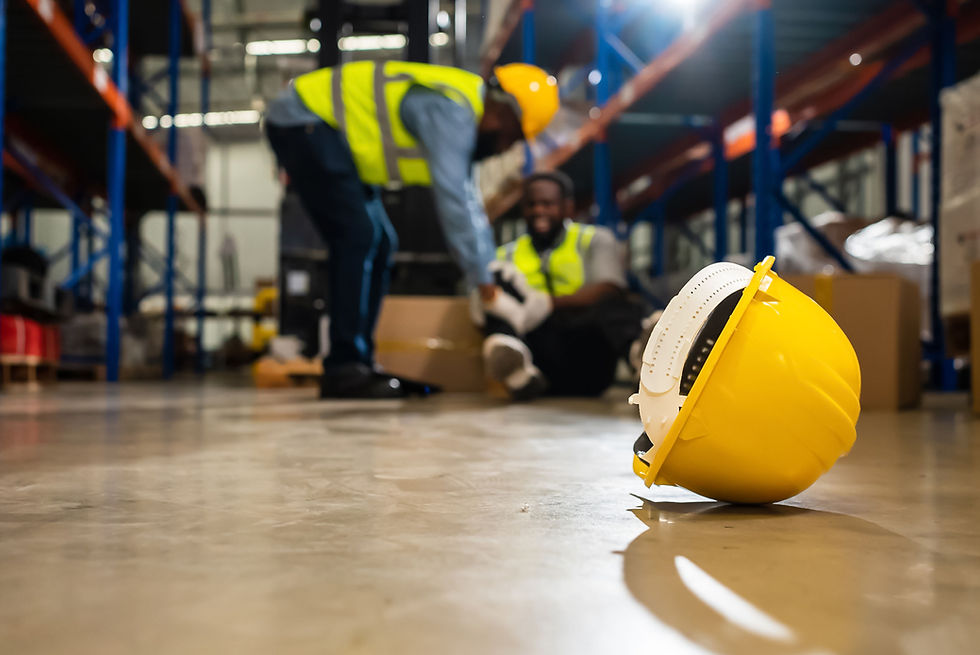
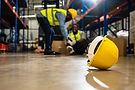
TEXAS INDUSTRIAL ACCIDENT LAWYERS
ADAME GARZA LLP
If you or a loved one has been hurt in an industrial accident, you could be facing a number of financial burdens. You may be feeling overwhelmed at the prospect of seeking compensation, but the Houston, Texas industrial accident lawyers at Adame Garza LLP have the experience to confidently help you. We have helped hundreds of workers recover their costs after an accident, and we can analyze your situation to see what options may be available to you.